Metod projektowania jest co najmniej kilka, zaczynając od programów komputerowych, które po wprowadzeniu do nich danych robią symulację, po przez własne symulacje opierając się na zależnościach matematycznych, co jest fajnym wyzwaniem (osobom nie będące za pan brat z matematyką wyższą odradzam), aż po projektowanie ?na oko?, co jest niestety, lub nie, powszechną praktyką. Po poznaniu kilku założeń, uproszczeń i odrobinie wprawy można ten ostatni sposób zacząć stosować.
To od czego zależy ten rozpływ i jak on wygląda? Są cztery czynniki które na niego wpływają:
- odległość ? na jaką ma popłynąć żywica ? rozpływ zwalnia wykładniczo wraz ze wzrostem odległości, tzn. im dalej od źródła znajduje się żywica tym wolniej zaczyna płynąć, aż do zatrzymania.
- lepkości żywicy ? im mniejsza lepkość tym łatwiej przesącza się żywica, punktem odniesienia może być porównanie do konsystencji wody.
- przepuszczalność ? medium w którym dystrybuowana jest żywica, im lepszy jego parametr tym łatwiej płynie w nim żywica, może być to siateczka rozpływowa, lub specjalna przekładka.
- różnica ciśnień ? między punktem dostarczającym żywicę, a punktem odsysającym powietrze (dostarczającym próżnie).
Natomiast cała zależność wygląda tak:
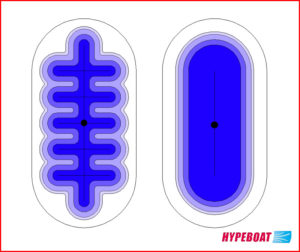
- rurki spiralne rozprowadzające żywice mają nieskończenie wielką przepuszczalność w stosunku do medium rozpływowego ? dostarczają cały czas wystarczająca ilość żywicy niezależnie od zasilanego pola powierzchni.
- rurki napełniają się błyskawicznie zanim jeszcze medium zacznie rozprowadzać żywice ? wszędzie start w tym samym momencie.
- ułożenie zbrojenia (poziomo, czy pionowo, zasysanie w górę, czy w dół) nie ma znaczenia.
- odsysanie w każdym punkcie kołnierza ma jednakową siłę.
- wszędzie jednakowa warstwa zbrojenia (brak zakładek).
Z takimi oto drobnymi przekłamaniami możemy zacząć projektowanie pierwszego przybliżenia rozpływu. Wybieramy układ który będzie dla nas najlepszy. Równoległy wymaga najmniejszej obsługi w trakcie podawania żywicy, ale potrzebna jest większa wprawa w układaniu. Szeregowy jest prostszy w projektowaniu, ale trzeba w odpowiednich momentach zmieniać punkty dostarczania żywicy. Po wyborze układu, ustalamy z wcześniej przeprowadzonej próby, bezpieczna odległość na jaką żywica może spokojnie dopłynąć. Można przyjąć 2/3 maksymalnego dystansu, jak widać na wcześniejszym wykresie do tego punktu żywica jeszcze dostatecznie szybko dociera. Z tą wiedzą projektujemy układ tak, żeby zakryć całe pole powierzchni kołami o promieniu naszego maksymalnego dystansu.
Szeregowy (oczkowy) |
Równoległy (krzyżowy) |
– zalety: łatwo przewidywalny rozpływ, kontrola etapów wtrysku ? sekwencyjność, bezpieczeństwo przy większych powierzchniach – wady: kontrolowanie etapów, kilka punktów do podawania żywicy, przez co łatwiej o wpuszczenie powietrza pod worek |
– zalety: jeden punkt wtrysku – wady: możliwość zamknięcia powierzchni, występowanie miejsc które znajdują się dalej od rurek niż inne, dedykowany do mniejszych powierzchni |
Jak widać cały proces nie jest magicznie skomplikowany, lecz możliwy do przewidzenia, a co za tym idzie wykonalne jest samodzielne jego zaprojektowanie. Otwiera nam to drogę do wdrożenia infuzji i skorzystanie z jej niewątpliwie licznych zalet. Powodzenia!
Maciej Wieruszewski
www.modele-cnc.pl
Zezwalam na przedruk tego artykułu w niezmienionej formie z podaniem linku zwrotnego.
Bardzo fajne zródło informacji.
A jak z doborem pomy próżniowej ? Czy są jakieś przeliczniki wydajność/m2 formy ?
Jan.
Dziękuje. 🙂
Pewnie są, ale jak jest zbiornik wyrównawczy/pośredni to wydajność nie jest już taka ważna.
Przy większych formach, będzie się po prostu dłużej czekało na uszczelnienie całej membrany. Im więcej przecieków tym dłużej.
Po sprasowaniu zbrojenia panuje mniej więcej stała próżnia pod workiem, a przepływy są znikome.
Całą prace wykonuje różnica ciśnień.
Wniosek – ważniejszym parametrem jest poziom maksymalnego podciśnienia.
nie pierwsza folia to 0.9 bar druga to 0,8 a trzecia zamykająca produkt to 0,7 bara, aby przyspieszyć vacum można zwiększyć na 3-ciej do 1, bara, oczywiście minus.
A ciśnienie musi być takie same wszędzie , w innym przypadku masz dziurę w foli i produkt nie będzie dobrze zalany, możesz całą pracę do śmietnika wrzucić.
Dziękuję za pożyteczne porady.
Początkującemu takiemu jak ja zawsze mogą bardzo pomóc.
Pozdrawiam i polecam się .
Robert.
Witam jaką najlepiej użyć żywice do laminowania próżniowego i gdzie można kupić ? .:)
Witam,
najczęściej używa się dedykowanych do tego celów epoksydów, ale i na innych, łatwiej dostępnych, które są dostateczne mało lepkie też można sobie poradzić.
Jednocześnie należy pamiętać, aby przy układzie równoległym (krzyżowym) nie tworzyć odgałęzień schodzących się do środka. Spowoduje to zamknięcie suchych powierzchni, które zostaną uwięzione (jak je uratować napiszę w kolejnym artykule z tego cyklu).
No to jaka jest metoda na uratowanie suchych miejsc ???
Są przynajmniej dwie. W zależności, czy jest to duży obszar, czy mały, to stosuje się zastrzyki z żywicy, lub dodatkowy punkt odsysania.
Zastrzyki można wykonać po przez naklejony pasek folii uszczelniającej (butylu) na worek, dużą strzykawką z igłą.
Drugą metoda stosuje się w wypadku zamknięcia dużych powierzchni, należy przygotować uszczelniony lejek podłączony do podciśnienia. Wtedy to nacinamy folie na środku obszaru zamkniętego i przyklejamy lejek – żywica powinna być dociągnięta do tego punktu.